Investment casting is a modern casting method that uses a wax pattern to create complex parts that are difficult to achieve with traditional casting techniques. The wax pattern is then invested in a heat-resistant material to form a mold. After the wax is melted and removed, molten metal is poured into the mold. Once the metal cools and solidifies, it takes the shape of the desired part. Finally, the ceramic mold is broken away, and the finished product is completed. To gain a better understanding of the investment casting process, please follow the article below.
Step-by-step overview of the investment casting process
Investment casting process includes steps such as wax pattern preation, shell building, wax removal, metal pouring, cooling and shell removal, cooling and shell removal.
Wax pattern preation: The process begins with the creation of a wax pattern, which is an exact replica of the desired final product. These patterns can be produced through injection molding, ensuring consistency and precision.
Shell building: The wax pattern is coated with a ceramic shell. This is done by dipping the pattern into a liquid ceramic material and then applying sand to create a robust outer layer. This shell is cured to harden, forming a strong mold.
Wax removal: Once the shell is fully cured, the wax is melted and drained away, leaving a hollow cavity in the shape of the part. This is typically done using heat, ensuring complete removal of the wax without damaging the shell.
Metal pouring: After the wax is removed, molten metal is poured into the cavity of the ceramic shell. This step requires precision in temperature control to avoid defects in the final product.
Cooling and shell removal: The metal is allowed to cool and solidify within the mold. Once cooled, the ceramic shell is broken away, revealing the cast part.
Finishing: The final step involves removing any excess material and finishing the part to meet specific surface quality requirements. This may include machining, polishing, or coating.
Advantages of the investment casting process
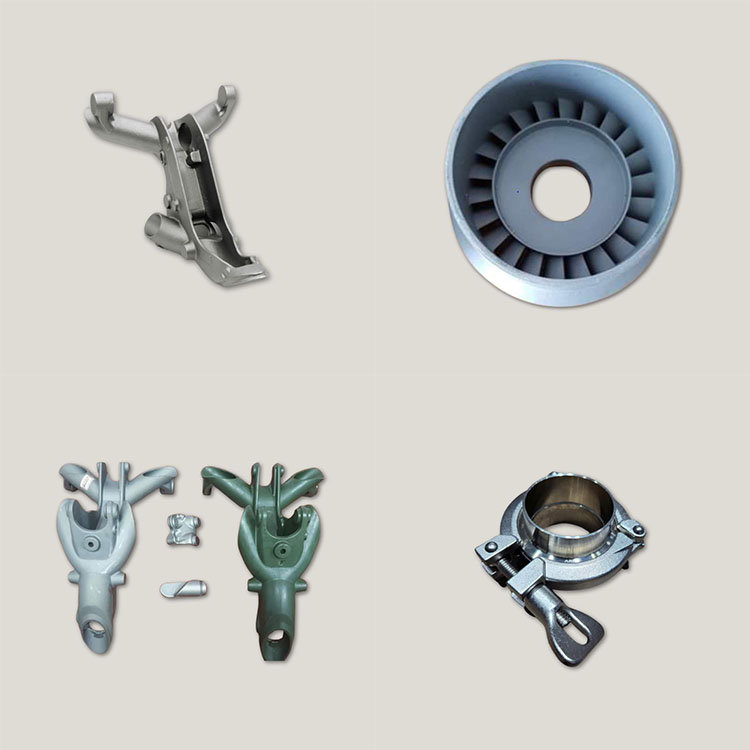
Investment casting process: Revolutionizing manufacturing with precision
The investment casting process offers several advantages:
- High precision: This method allows for exceptional dimensional accuracy, making it ideal for components that require tight tolerances.
- Complex geometries: It can produce intricate shapes that are difficult or impossible to achieve with traditional casting methods.
- Material versatility: A wide range of metals can be used, including alloys that enhance the performance of the final product.
- Reduced waste: The process minimizes material waste, making it a cost-effective option for high-quality production.
The investment casting process is a powerful manufacturing technique that combines precision, complexity, and efficiency. Its ability to produce high-quality parts makes it a preferred choice in many advanced industries. By understanding this process, companies can make informed decisions about their manufacturing needs and harness the advantages that investment casting offers. Whether you’re looking to produce intricate aerospace components or reliable automotive parts, investment casting GTR Vietnam Cast provides a solution that meets the highest standards of quality and performance. Contact us immediately for the best advice and support.
See more:
Contact GTR Vietnam immediately for free consultation:
Address: Hall X2, Hai Thanh industrial zone Duong Kinh ward Hai Phong, Vietnam
Website: https://gtrvietnamcast.com/
Email: info@gtrvietnamcast.com
Hotline: +84 2253 660919